The Bodycare NZ blog
Useful info and resources
on workplace health & safety in New Zealand
How to keep your workplace healthy and safe
Articles and resources from our team of experts
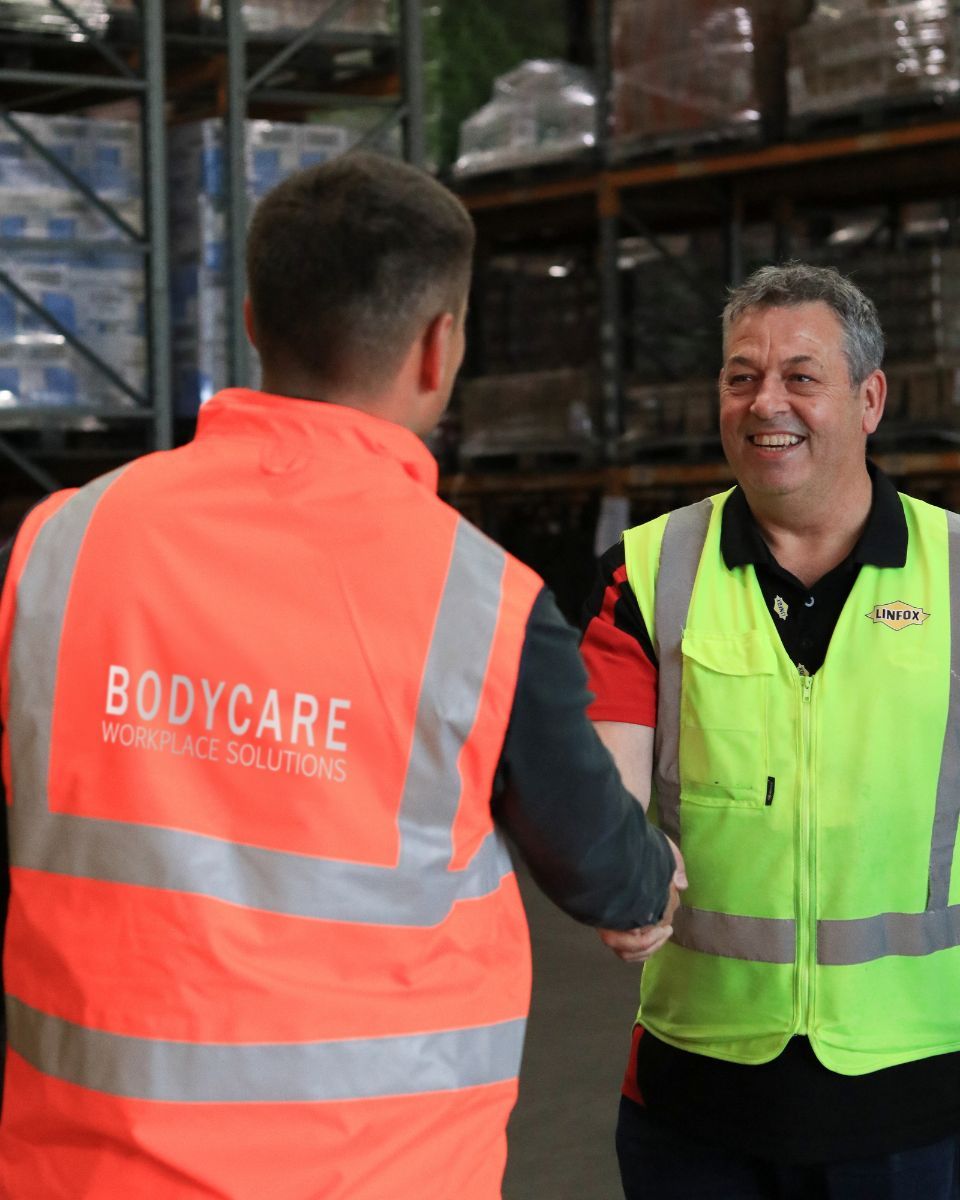
Developing a well-rounded approach to employee health and safety is the key to ensuring a healthy and safe workplace. In addition to the negative impact being injured or ill can have on an employee, the greater economic burden that absenteeism, lost productivity and workers’ compensation claims has on your business can also be devastating. With the World Day for Safety and Health at Work just around the corner, there’s never been a better time to consider protecting the wellbeing of your workers and organisation through strategic corporate health and safety initiatives. Manual handling Workplace manual handling injuries cost the Australian economy $28 billion per year, with employers and workers bearing a combined 82% of this cost. Unfortunately, many employers only think of manual handling as being limited to only a few areas within a worksite, when in reality, nearly all jobs require some form of manual handling. For instance, tasks such as stacking stationery onto shelves in a supply room or dressing mannequins in a shop front – while many don’t realise, even tasks like these require manual handling, which if performed incorrectly, can lead to injury. As an employer, it’s your responsibility to ensure that you and your employees are educated in best-practice manual handling techniques to avoid injury and workers’ compensation claims. To make sure that you are adhering to the latest Safe Work Australia guidelines, it’s important to have a professional Manual Handling Training Program in place. Bodycare can tailor a program to suit the requirements of your organisation, giving you and your employees the tools to identify and mitigate manual handling risks in your workplace. Ergonomic workspaces One in five of workers’ compensation claims now relate to musculoskeletal injury, making ergonomically correct workplaces a priority for employers wanting to avoid injury-related absenteeism and lost productivity. In order to avoid injury, the design and systems of your workplace must fit the user. This could mean providing a quality desk chair that supports the lower back, or a standing desk to ensure employees have the opportunity to move around throughout the workday. For organisations working on a hybrid or remote working model, there are additional challenges to ensuring a safe working environment for employees, particularly around the optimal ergonomic set-up. Employers not only have a legal responsibility to ensure that their employees’ health and wellbeing is not compromised in the workplace, they also need to ensure their workers are safe while working from home. Due to many employees having a lack of supportive equipment in the home workspace, the potential for musculoskeletal injuries is unfortunately significantly exacerbated, predisposing employers to an increased likelihood of claims and cost of doing business. Thankfully there are ways to mitigate these risks. By simply providing employees with the appropriate guidance and expert advice, they have the tools to optimise their home working environment and can remain symptom-free. To ensure your employees’ workspaces are correctly set up both in the office and at home, Bodycare’s team of Occupational Health Professionals can perform in-office or virtual ergonomic assessments and make simple, practical and cost-effective recommendations on how to improve office and home working setups through one of our ergonomic workshops or one-on-one consultations. Mental health Each year $480 million dollars is paid out for work-related mental health disorders, costing the Australian economy dearly due to lost productivity and absenteeism. Despite this, awareness for mental health safety has severely lagged behind that of physical health. This may be due to the stigma still attached to mental health issues, or it may be because some employers simply don’t know where to start when it comes to implementing preventative strategies to look after their employees mental health and wellbeing. If you are just starting out, here are a few mental health initiatives you can consider implementing into your organisation: Educational seminars Workplace mental health training Employee assistance programs Flexible work hour arrangements Return to work policies for staff experiencing mental health conditions To truly tackle mental health head-on, a tailored mental health seminar or program may be the best for your organisation. Bodycare’s mental health experts can customise a specific seminar or mental health program to meet the specific needs of your industry. All of our seminars can be held virtually, onsite or in-office. These programs give management and employees the tools to spot signs of poor mental health in each other and look after themselves, so that everyone can flourish at work. Diet and Exercise Australia is one of the world’s most overweight nations and it’s causing serious issues for employers who rely on a healthy workforce to minimise the burden of productivity loss and absenteeism. The good news is that the workplace has been shown to be the perfect environment to initiate lifestyle changes, meaning you can make a big difference to the health of your workforce just by making simple changes at work. As an added bonus, healthy eating and exercise has shown to boost creativity and productivity in the workplace. Initiatives you can implement in your workplace include: Supplying healthy snacks like fruit, nuts and sparkling water Encourage walking meetings Offer virtual fitness challenges Team up with local healthy restaurants to offer staff discounts Educational seminars around making nutritious choices Subsidise gym or fitness app subscriptions Implement standing desks For those working from home, the best way to improve the health and wellbeing of your workforce is through pragmatic education. Bodycare’s health and wellness experts can tailor a corporate wellness program to the unique requirements of your organisation and deliver through virtual or onsite seminars and webinars. We cover topics such as: Nutrition for Wellness Healthy Fast Food Foods to Boost Your Mood Creating Healthy Habits Women and Men’s Health We also offer a range of health programs and challenges such as: Yoga and Pilates Meditation and mindfulness Virtual wellbeing and fitness challenges Group fitness Corporate/Group challenges If you’re not sure where to start or what the right health and wellbeing solution is for your business, contact Bodycare to organise a strategic health risk appraisal and we can design the right program for you. An organisation is only as healthy as its employees, so making an investment in their wellbeing is an investment in your business. By introducing a range of initiatives into your organisation, you are able to provide education and support to your team, reducing the chance of illness or injury occurring in your workplace. This is why having a multi-faceted, well-rounded approach to health and safety is imperative in any business.
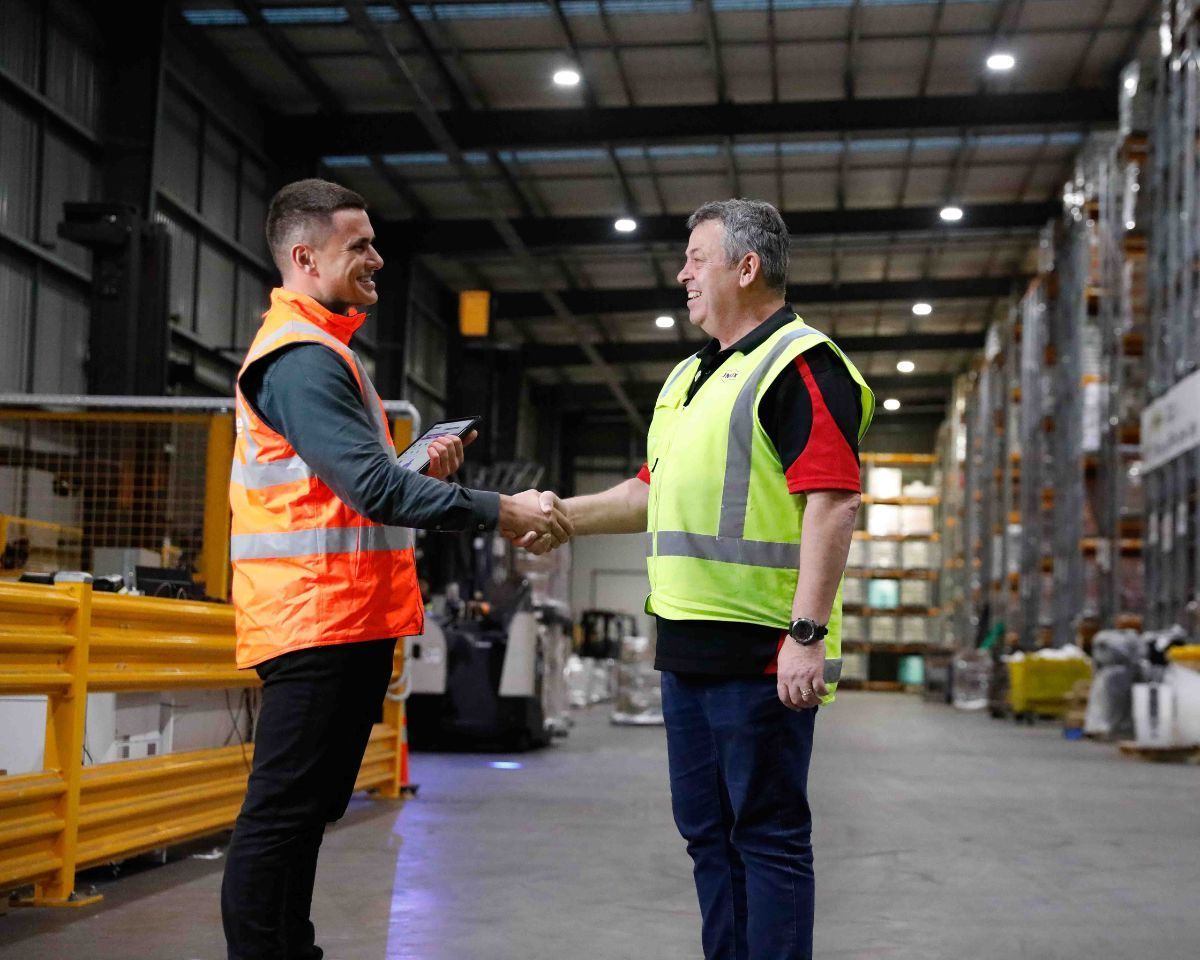
Despite efforts to prioritise health and safety in the workplace, risk of incident or injury that result in workers’ compensation claims are, to an extent, inevitable. There are however several ways to lower the risk and in turn lower the number of these claims. Below are some strategies to help your business avoid workers’ compensation claims in a proactive methodical way that will also enhance your overall health and safety program.
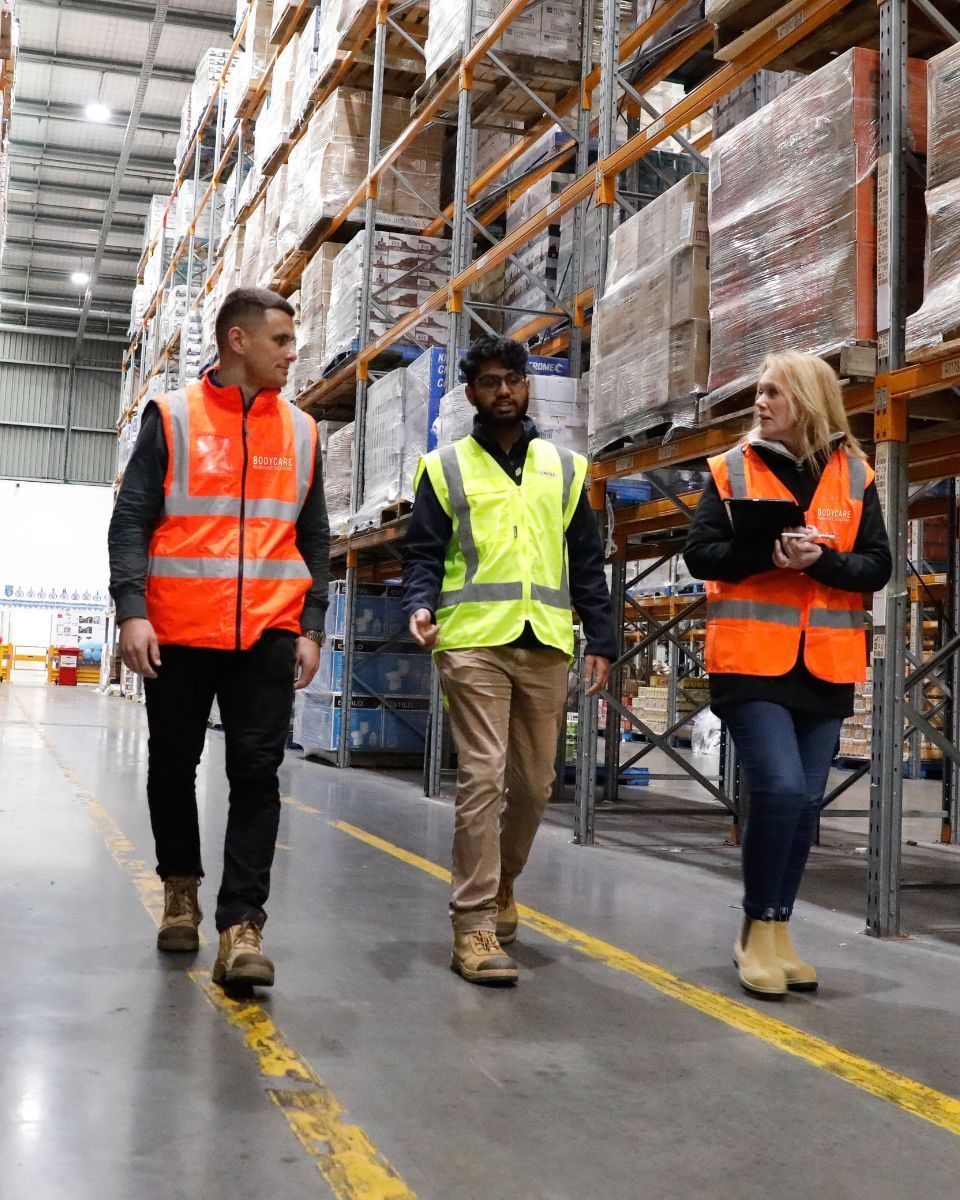
Wouldn’t it be great if you could receive an accurate prediction about who was going to succumb to a musculoskeletal injury next at your workplace and over the next two years? Think about it: wouldn’t you like to know who’s next to get carpal tunnel syndrome? Or who will experience shoulder muscle strains or a nerve root impingement in the neck? How about a lower back disc bulge? Hold up, hold up. Put the phone down – you don’t need to make any calls to uncover this information. You can achieve this with an early intervention program.